New membrane elements allow a reverse osmosis (RO) system to operate optimally with the highest removal of dissolved salts (also known as salt rejection) and the greatest production of permeating water at its design pressures. With time, these performance characteristics will decline to a point where it may be necessary to replace the RO membrane elements. Because many facilities depend on the RO for meeting their purified water needs, anticipating when the membranes are going to need replacement may be critical to the plant’s operation.
The membrane manufacturers will usually prorate their membrane warranty over three years, although it is rare for a membrane failure to occur because of its manufacture. Possibly related to the length of the manufacturer’s warranty, three years of life has become a common expectation for membrane replacement. Water Purifiers Reverse Osmosis
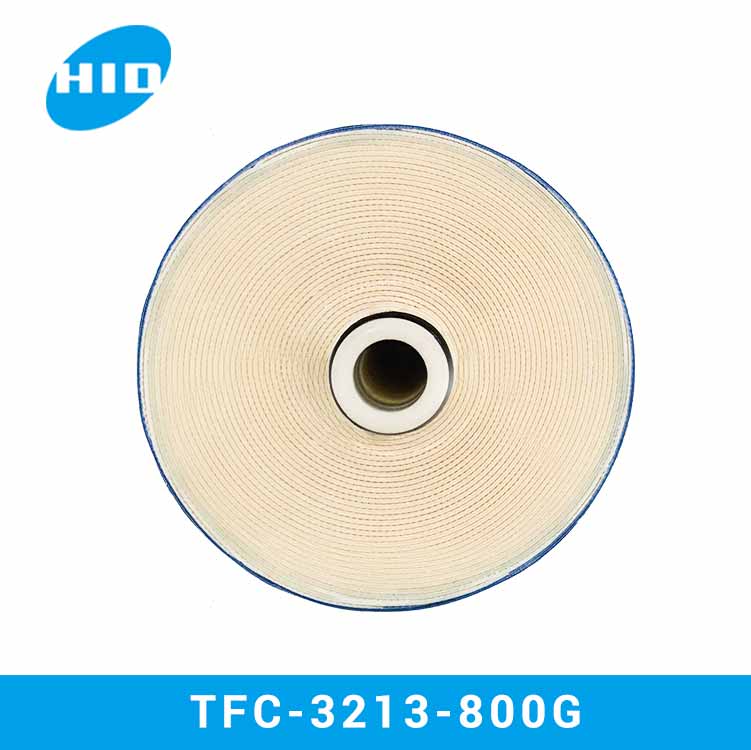
It should be noted an RO membrane element is not a filter, which means it is not a disposable device expected to foul up or wear out due to its use. While it is true the RO membrane will not last forever, there are cases where the membranes have operated for more than 10 years without suffering significant and permanent changes in their performance.
An RO membrane does not perform like a filter. All the incoming water is not forced through the membrane sheet so the suspended solids are always left behind as particles stuck on the surface. With a well-designed RO system, the majority of the suspended solids in its inlet water will pass through the membrane elements and exit the system with its concentrate stream. This can be verified by measuring the suspended solids in the concentrate stream relative to their concentration in the inlet stream and noting how their increased concentration correlates with the concentration factor ratio of the inlet flow divided by the concentrate stream flow rate.
A well-designed RO system is one whose pretreatment equipment removes large particles and reduces the concentration of smaller particles sufficiently to keep the RO fouling rate moderately low. It may not be economical to eliminate RO fouling by designing the water system with extensive upstream filtration equipment and a low RO permeate flux rate. However, with a high concentration of suspended solids in the raw water, it is usually practical to at least include a multimedia filter in its pretreatment. It may be possible to justify the inclusion of a membrane filtration system, like a microfiltration or ultrafiltration system, upstream of the RO, which will then enable an increased RO permeate flux rate and still reduce the RO fouling rate. The RO will then require infrequent chemical cleanings to maintain its performance.
Some of the suspended solids may be biological in nature, originating in the water source or created in the water pretreatment system itself. If bio activity is not controlled within the piping and treatment components upstream of the RO, the RO pretreatment may become the source of biological fouling particles. These biological particles often have an affinity for attaching to the RO membrane, which may make it difficult to keep them from fouling the membranes even with a low rate of permeation. It may be necessary to employ a method for controlling this activity, such as with frequent biocide shock treatments or sanitizations at the source of these bio particles.
A common method for monitoring this pretreatment effectiveness is with the silt density index (SDI). The SDI value in the RO inlet water will often correlate with the required RO cleaning frequency. A common SDI target is less than five, which then results in the need for RO cleaning less than five times per year.
However, this correlation with SDI will only occur if the RO is designed with moderately low permeation rates throughout the system. The most critical region of the RO system where fouling by suspended solids is most likely to occur is where the water first enters the RO membranes since this is where the water permeation rate is the highest. As the feedwater flows across the membrane surface and through the membrane elements, the membrane pressure will decline.
The choice of RO membrane may impact this fouling rate. When low-energy membranes are used with a warm, low-salinity water source, it may be impossible to prevent the inlet-end membrane elements from permeating water at a rate far greater than the elements located at the concentrate end of the RO system. For example, the membrane feed pressure may be as low as 80 pounds per square inch (psi), so if there are 40 psi of pressure losses as the water passes through the RO membranes on its way to the concentrate exit stream, the concentrate-end membrane pressure may only be 40 psi, and the concentrate-end membrane elements will be producing less than half the permeate flow rate of the lead-end membrane elements.1
Low-fouling RO membranes are available that are more resistant to the initial adhesion of fouling particles to the membrane surface. This may delay the initial fouling of the RO membranes and should be considered for use in many fouling applications.2 Also in fouling applications, the selected membrane model should use a 34-mil (thousands of an inch) feed-to-concentrate spacing material, which is less prone to plugging off its flow channels by larger particles and is better able to be cleaned.3 Maximize Life of RO Membranes
Even if the pretreatment or the RO design is not ideal, cleaning the RO before the fouling solids become overly stabilized is another method to indefinitely extend membrane life. Even frequent cleanings will not damage the membrane if aggressive cleaning agents do not need to be used in fully restoring original RO performance.
With a high RO fouling rate, a common error is to go too long before cleaning. If the fouling solids become overly compressed against the membrane, they will become less responsive to the cleaning solution. The inability to fully restore the original membrane performance means fouling solids are being left behind. After returning the RO to service, these remaining solids will often cause the membranes to experience an increased fouling rate due to blocked flow channels or possibly because of the suspended solids having a greater attraction to the compacted fouling solids coating the membrane polymer surface.
As the fouling becomes more severe, the fouling solids impede the ability of dissolved salts to diffuse back from the membrane surface, resulting in increased salt passage into the permeate stream. Either poor salt rejection or low permeate production can then result in the need to replace the membrane elements. When severe fouling blinds off enough of the membrane flow channels, the result can be a high feed-to-concentrate pressure differential (greater than 60 psi differential) across the membrane elements, which may be sufficient to crush the concentrate-end elements.
With low salinity water, the rate of water permeation will be roughly proportional to the membrane pressure.
“Improve RO system performance and reduce operating cost with FilmTec fouling-resistant (FR) elements,” J.A. Redondo, Desalination, Nov. 1999, pp. 249-259
“Effect of feed spacer thickness on the fouling behavior in reverse osmosis process — A pilot scale study.” Hyung-Gyu Park, et al., Desalination, Feb. 2016, pp. 155-163
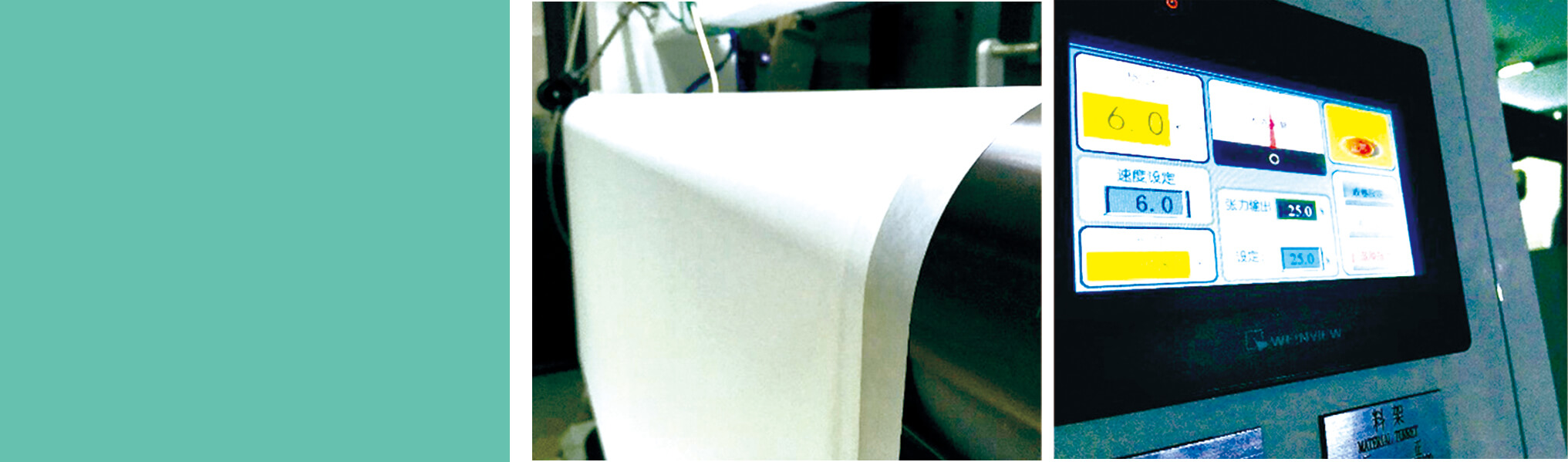
RO Membrane Wholesaler Wes Byrne, a consultant for Kurita America, has more than 43 years of experience in the design, operation and maintenance of reverse osmosis systems and is the author of Reverse Osmosis, A Practical Guide for Industrial Users, 2nd Edition (Tall Oaks Publishing). He has worked with thousands of RO systems around the world and has trained thousands of operational personnel.