We use cookies to enhance your experience. By continuing to browse this site you agree to our use of cookies. More info.
In 2014, Ford used mostly aluminum to build the body of the popular truck F-150, resulting in an overall weight reduction of the vehicle by approximately 700 pounds. This modification was designed to increase gas mileage and save fuel money at the pump. Aluminum Cold Drawn Pipe

It is possible to further reduce the weight by using advanced aluminum alloys for roof rails, subframes, crossbeams, and other structural parts. But that has not occurred as these alloys are costly due, partly, to their sluggish manufacturing rates using conventional extrusion processes.
However, these advanced alloys recently achieved a personal best, using an innovative, new method to extrusion that significantly increases their manufacturing speed. Shear Assisted Processing and Extrusion (ShAPE™) uses considerably less energy and can produce a product at over ten times the rate of conventional extrusion, with no compromise in quality.
Besides, it can also enhance the mechanical properties of the aluminum alloy, called alloy 7075. Alloy 7075 possesses a strength-to-weight ratio 85% higher than the alloys placed in standard passenger vehicles; however, manufacturing costs are around 30% more expensive than the “6000 series” alloys typically used.
That price differential is acceptable in aerospace applications, where lighter weight materials trump higher costs in order to achieve better fuel efficiency, improved maneuverability, and lower launch cost. But in vehicles, it’s a limiting factor that we hope to change.
Scott Whalen, Materials Scientist and Developer of ShAPE, Pacific Northwest National Laboratory
This high cost is predominantly because of alloy 7075 being extremely hard to extrude into structural parts. Indeed, 7075 is extensively seen as the toughest to extrude than all of the commercial aluminum alloys.
Conventional extrusion of 7075 is very slow and involves painstakingly striking solid metal through a die. The slow extrusion speed of merely 1 to 2 m (3 to 6 ft) per min—combined with higher energy necessities—renders 7075 costlier than the 6000 series aluminum alloys, which can be extruded at over 20 m (65 ft) per min.
ShAPE is a very energy-efficient extrusion method that delivers superior-quality products. A new study showed that it can also extrude high-strength aluminum alloys at a faster rate. The research findings can be seen in the November issue of the Journal of Manufacturing Processes.
Extensive testing shows that PNNL’s process can increase the speed by about 10 times that of conventional extrusion for this alloy, using about half the energy. Our process can extrude about 12 meters per minute with no tearing or cracking, whereas conventional extrusion is limited to about 1 to 2 meters per minute—and our process even enhances some material properties.
Scott Whalen, Materials Scientist and Developer of ShAPE, Pacific Northwest National Laboratory
Whalen is also the corresponding author of this study.
ShAPE can extrude wires, tubes, and bars with strength features that match crucial industrial ASTM criteria and ASM typical values. The elongation of alloy 7075—stretchability before it breaks—is 50% more than traditional extrusion, which can support energy absorption during a crash.
The patented ShAPE method incorporates rotational motion to conventional linear extrusion. It develops sufficient heat to heat the metal, causing it to flow and deform as it is forced via a die to form product shapes.
Scientists state that the capability to extrude at a lower temperature is one of the explanations for how ShAPE can accomplish production rates for alloy 7075 that would tear the material in traditional extrusion.
Besides increasing speed, the ShAPE method can also exclude the need for energy-intensive thermal treatment processes necessary for conventional extrusion, saving about 50% of the energy needed for extrusion of alloy 7075.
During the conventional extrusion process, large billets of metal must first be heat treated at temperatures of over 400°C (750°F) for nearly a day to homogenize, or consistently distribute, different elements like copper and magnesium throughout the alloy. ShAPE can extrude billets without homogenization, saving an estimated 5% on the overall cost of ShAPE-extruded products.
Furthermore, preheating in a furnace is necessary for conventional extrusion to soften the billet before extrusion. With ShAPE, preheating is not required, since all the required heat emanates from the process itself. Other post-extrusion thermal treatments are also excluded or minimized, resulting in overall 50% energy savings.
ShAPE’s increased extrusion speed, integrated with reduced energy use and, thus, lower carbon emissions, can make the lightweight 7075 alloy economical for the passenger vehicle market. In due course, lighter vehicles will also contribute to reducing carbon emissions for the transportation industry through better fuel efficiency for cars driven by internal combustion engines and extra mileage driving per charge for electric cars.
ShAPE is part of the solid phase processing collection of technologies, which are upcoming as a scalable, cutting-edge manufacturing method to manufacture metals and metal composites that are cheaper, greener, and better than those processed by traditional methods.
The ShAPE process for the manufacture of 7075 aluminum alloys was created with financial assistance from the Department of Energy Office of Energy Efficiency and Renewable Energy's Advanced Manufacturing Office.
Whalen, S., et al. (2021) High speed manufacturing of aluminum alloy 7075 tubing by Shear Assisted Processing and Extrusion (ShAPE). Journal of Manufacturing Processes. doi.org/10.1016/j.jmapro.2021.10.003.
Source: https://www.pnnl.gov
Do you have a review, update or anything you would like to add to this news story?
Dr. Craig Johnson & Dr. Kate Vanderburgh
AZoMaterials speaks with Dr. Craig Johnson, Director of Research Core Facilities, and Dr. Kate Vanderburgh, Scanning Electron Microscope (SEM) and X-Ray Microscopy Manager, about the Materials Characterization Core (MCC) facility at Drexel University.
In this interview, News Medical speaks with John Weaver from Pfizer about the importance of process safety testing.
In this interview, AZoM speaks to Bruker Optics about the different ways IR light can be used in semiconductors.
Specac’s Power Hydraulic Press Series are available in 8 Ton, 15 Ton and 25 Ton load configurations.
The SamplerSight Pharma from PMS is an easy-to-use software for batch sampling.
Allectra's latest bimetallic CF component series, featuring innovative Titanium CF Flanges linked with Aluminum Tubes, promises to revolutionize the design of Aluminum chambers.
The global semiconductor market has entered an exciting period. Demand for chip technology is both driving the industry as well as hindering it, with current chip shortages predicted to last for some time. Current trends will likely shape the future of the industry, which is set to continue to show
The primary distinction between graphene-based batteries and solid-state batteries lies in the composition of either electrode. Although the cathode is commonly changed, carbon allotropes can also be employed in fabricating anodes.
In recent years, the IoT is rapidly being introduced into almost all sectors, but it has particular importance in the EV industry.
AZoM.com - An AZoNetwork Site
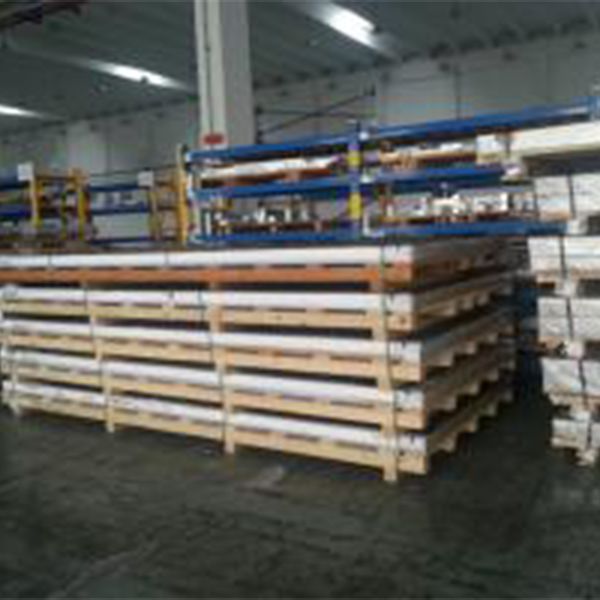
Round Aluminum Tubing Owned and operated by AZoNetwork, © 2000-2023